
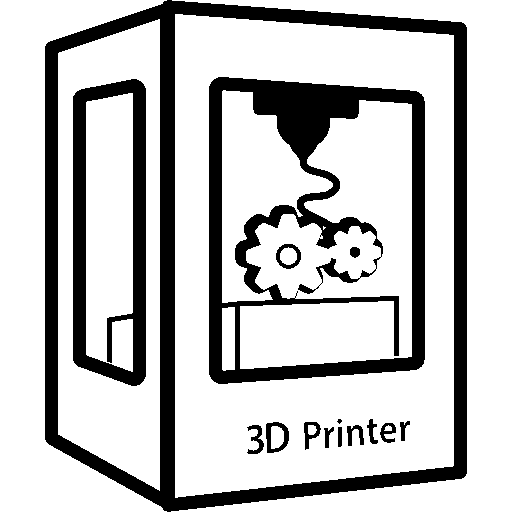
If you have an enclosure, I would say try out ASA. Similar to ABS, I’ve found it makes some really nice parts that are tough and UV resistant. Great for things you want to leave outdoors. Otherwise TPU is useful stuff too, and no heated chamber required. I was using it this weekend to print up seals and grommets for a trailer I’m rewiring. It’s nice being able to print up some parts I need rather than making a drive to the hardware store and hoping they’ll have something I can use.
Used to use Vent playing Eve Online 19 years ago. Worked great back then. Apparently it’s still around, but still no Linux support after all these years.